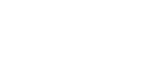
Understanding Rigid-Flex PCBs: A Comprehensive Guide to the Future of Circuitry
In the world of electronics, the demand for versatile, durable, and compact designs continues to grow. This has given rise to various innovations in printed circuit board (PCB) technology, with one of the most notable being the Rigid flex pcb. Offering the best of both worlds—rigid and flexible circuit boards—rigid-flex PCBs are becoming the go-to choice for a wide range of industries, from medical devices to consumer electronics, aerospace, and more.
If you're looking for rigid-flex PCBs or are simply interested in learning more about them, this article will provide a thorough understanding of their design, benefits, applications, and why partnering with a professional flex PCB manufacturer can ensure you get the highest-quality products for your needs.
What is a Rigid-Flex PCB?
A rigid-flex PCB is a type of printed circuit board that combines the best features of rigid and flexible PCBs into one unified design. It consists of both rigid sections (typically made from standard PCB material) and flexible sections (made from materials such as polyimide). These sections are integrated to form a single, cohesive unit. The rigid parts of the PCB provide support and stability, while the flexible parts allow for bending, folding, and conforming to various shapes and sizes.
This hybrid approach enables rigid-flex PCBs to be used in applications where both space-saving and reliability are crucial. The flexibility offered by these boards makes them ideal for compact, high-performance electronic devices that need to fit into tight spaces or endure mechanical stress and vibration.
The Structure of a Rigid-Flex PCB
1. Rigid Sections
The rigid sections of a rigid-flex PCB are typically made from standard PCB materials, such as FR4 or other composite substrates. These rigid areas house the more traditional components, such as connectors and complex circuitry. They provide mechanical support and ensure that the components remain fixed in place, preventing movement that could disrupt electrical connections.
2. Flexible Sections
The flexible sections are made from materials like polyimide, which allow the PCB to bend, fold, and twist. These sections enable the PCB to fit into spaces where traditional rigid PCBs cannot, such as in compact devices or intricate shapes. The flexible areas can also absorb shock and vibration, which is particularly beneficial in environments where physical stress is a concern.
3. Interconnections Between Rigid and Flexible Sections
The integration of rigid and flexible sections involves specialized techniques to ensure that the two components function seamlessly together. Advanced manufacturing processes are employed to create reliable electrical connections between the two types of substrates, such as through-hole plating or using conductive adhesive.
Key Advantages of Rigid-Flex PCBs
1. Space Efficiency and Design Flexibility
One of the most significant advantages of rigid-flex PCBs is their ability to fit into small, compact spaces without compromising performance. With the flexibility to bend and conform to specific shapes, they can be used in highly compact devices, making them an essential choice for industries that require miniaturization, such as medical devices, mobile phones, and consumer electronics.
2. Durability and Reliability
Rigid-flex PCBs offer superior durability and reliability compared to traditional rigid or flexible PCBs alone. The combination of rigid sections for support and flexible sections for adaptability ensures that the board can withstand mechanical stress, vibrations, and shocks. This makes rigid-flex PCBs ideal for mission-critical applications in industries like aerospace, automotive, and military technology.
3. Reduced Size and Weight
By integrating rigid and flexible elements into a single PCB, manufacturers can create designs that are not only smaller and lighter but also more efficient. The ability to combine multiple functions into a single board can help reduce the overall size and weight of a product, which is crucial in sectors such as consumer electronics, wearables, and portable devices.
4. Simplified Assembly
Rigid-flex PCBs can help streamline the assembly process by reducing the number of components and interconnections required. Instead of having separate rigid and flexible boards connected by wires or connectors, a rigid-flex PCB combines both elements into a single unit. This simplification can lower the overall cost of manufacturing and reduce the risk of errors during assembly.
5. Improved Thermal Management
Rigid-flex PCBs often feature advanced thermal management capabilities. The rigid sections help dissipate heat effectively, while the flexible sections allow for the natural flow of air or cooling systems within compact designs. This combination ensures that the PCB can operate efficiently in temperature-sensitive environments.
Applications of Rigid-Flex PCBs
1. Medical Devices
In the medical field, space-saving and durability are paramount. Rigid flex pcb are commonly used in medical devices such as diagnostic equipment, implantable devices, and wearable health monitors. These boards offer the flexibility to fit in the limited space within medical devices while maintaining high reliability.
2. Consumer Electronics
The demand for compact, high-performance consumer electronics continues to rise, with devices like smartphones, tablets, and wearables needing to fit into smaller and smaller spaces. Rigid-flex PCBs are used extensively in these devices, offering the necessary performance and flexibility to support complex circuitry in tight spaces.
3. Aerospace and Defense
In aerospace and defense applications, rigid-flex PCBs are used in satellite systems, avionics, and other mission-critical electronics. These boards must withstand harsh environmental conditions, including extreme temperatures, high vibration, and physical shocks, making the durability and flexibility of rigid-flex PCBs essential for these applications.
4. Automotive Industry
The automotive industry uses rigid-flex PCBs in applications such as electric vehicles (EVs), advanced driver-assistance systems (ADAS), and infotainment systems. These boards can handle the demanding conditions of the automotive environment, offering resistance to temperature fluctuations, vibrations, and potential damage from impact.
5. Industrial Equipment
Industrial equipment often requires ruggedized and compact designs to operate efficiently in challenging environments. Rigid-flex PCBs are used in industrial machinery, robotics, and control systems where space is limited, and the system needs to endure physical stress and harsh working conditions.
Why Choose a Professional Flex PCB Manufacturer?
1. Expertise in Advanced Manufacturing Techniques
Manufacturing rigid-flex PCBs requires specialized knowledge and expertise in both flexible and rigid PCB technologies. A professional flex PCB manufacturer has the experience and tools necessary to produce high-quality rigid-flex PCBs that meet the strictest standards of durability, performance, and reliability.
2. Precision and Quality Control
A professional manufacturer ensures that every rigid-flex PCB is produced with precision, minimizing defects and ensuring the highest quality. Advanced testing and quality control processes are essential to ensure that the boards meet industry standards and perform as expected in real-world applications.
3. Custom Design Capabilities
Every project has unique requirements. A professional manufacturer can work closely with you to create custom rigid-flex PCBs that fit your specific needs, whether it’s for a consumer product, medical device, or industrial system. This customization can include changes to the board layout, material selection, and other design features.
4. Timely Delivery and Support
A reputable flex PCB manufacturer will also provide timely delivery of high-quality products and offer ongoing support throughout the lifecycle of the product. This includes assistance with design revisions, troubleshooting, and advice on the best practices for assembly and integration into your final product.
Conclusion
Rigid-flex PCBs are an essential innovation in the world of electronics, offering the benefits of both rigid and flexible circuit boards in a single, integrated design. Whether you're working in consumer electronics, medical devices, aerospace, automotive, or any other industry, rigid-flex PCBs offer unparalleled durability, compactness, and reliability. By partnering with a professional flex PCB manufacturer, you can ensure that you receive top-quality, custom-designed rigid-flex PCBs that meet your specific needs and perform flawlessly in your applications.